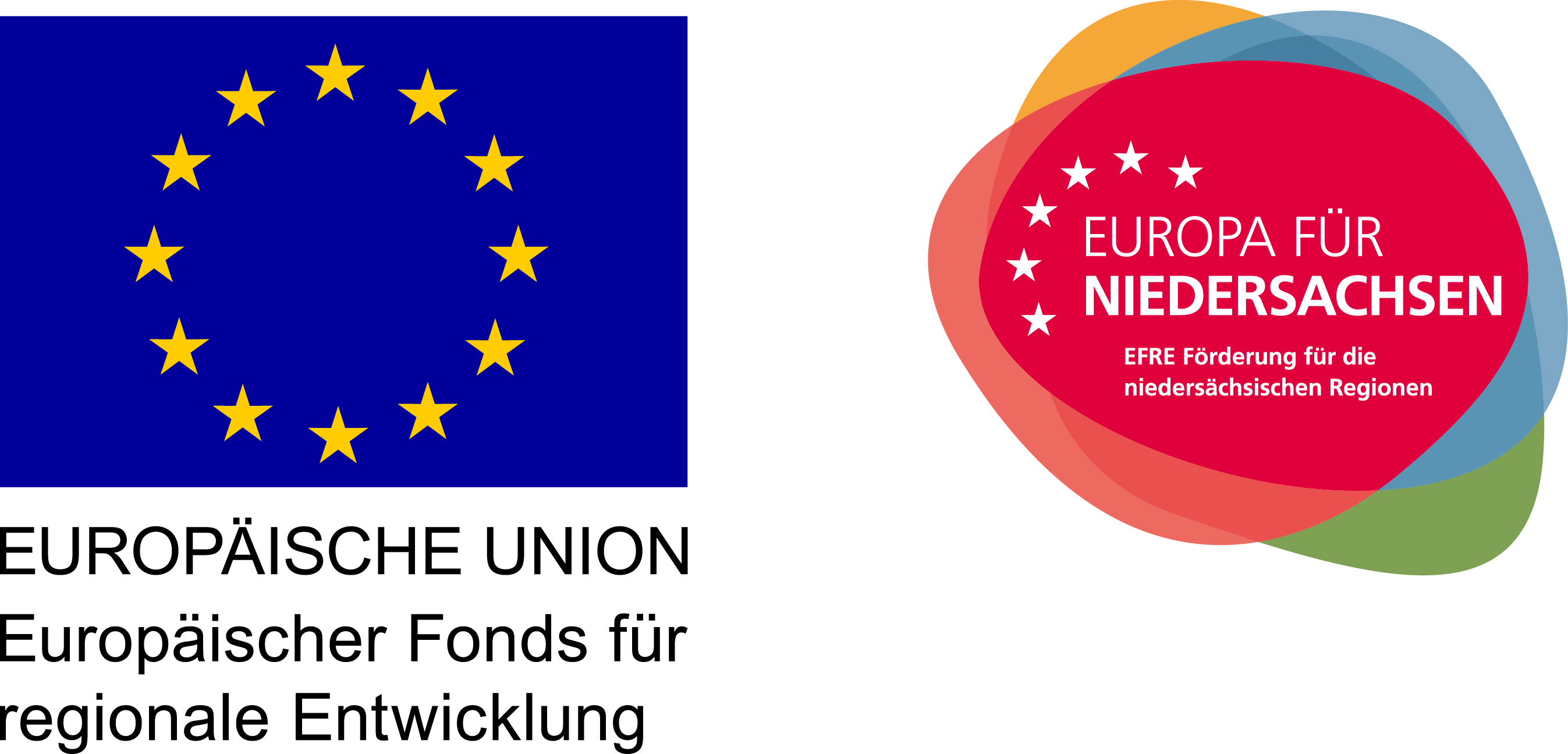
IFA - Antriebstechnik - Forschung
Bei den Problematiken geht es hauptsächlich um:
Grundidee
Die Grundidee der VDS hat es zum Ziel, die hohen Betätigungskräfte des VVS-Systems, welche aufgrund der translatorischen Bewegung des Tellerventils erforderlich sind, zu reduzieren. Dies soll durch drehbare Ventile bzw. Drehschieber ermöglicht werden. Dadurch soll ein hydraulisches System zur Betätigung der Ventile überflüssig werden.
Die Herausforderungen dieses Forschungsprojektes lassen sich grundsätzlich in zwei Themenblöcken zusammenfassen.
Erstellung CAD Modell des Prototypen
Die Erstellung des CAD Modells des Prototypen hatte die Überführung des Konzeptes in eine
geometrisch definierte Baugruppe zum Ziel. Dies war essenziell für sämtliche weitere
durchzuführende Meilensteine und wurde für die lineare als auch für die rotatorische Version
des
Aktuators durchgeführt.
Bewegungssimulation
Auf Basis der generierten CAD Modelle wurden Bewegungssimulationen
durchgeführt, welche eine Analyse der generierten Aktuatorauslenkung zum Ziel hatte.
Konkretisierung sämtlicher Bauteile des Prototypen
Auswahl des Piezosystems und der Werkstoffe
Der Auswahl des Piezosystems gingen zahlreiche Berechnungen und Abstimmungen mit
nationalen und internationalen Herstellern derartiger Systeme voran. Letztendlich wurde sich
für
das d-Drive System der Firma Piezosysteme Jena entschieden, da dieses System unseren
technischen als auch finanziellen Anforderungen gerecht wird.
Die ausgewählten Komponenten ermöglichen eine Steuerung oder eine Regelung der
Piezoaktuatoren und somit der angestrebten Aktuatoren bis zu einer Arbeitsfrequenz von 100Hz.
Zusätzlich verfügt dieses System über einen integrierten Funktionsgenerator, welcher
Untersuchungen des linearen bzw. rotatorischen Aktuators unter dem Einfluss dynamischer
Belastung ermöglicht.
Rapid Prototyping Modell des Prototypens des Hochgeschwindigkeitsaktuators
Wie bei der Definition der Meilensteine des Projektes beschrieben, soll nach Definition des
finales
CAD Modells und vor der mechanischen Fertigung ein Rapid Prototyping Modell des Aktuators
erzeugt werden. Dies wurde für den linearen als auch für den rotatorischen Aktuator
durchgeführt.
Durch diese Vorgehensweise können Fehler in der Definition des CAD Modells detektiert werden
und erste Eindrücke über die korrekte Funktion des Konzeptes gewonnen werden. Da das
Erzeugen eines 3D Modells deutlich unkomplizierter und kostengünstiger ist als die
mechanische
Fertigung ist diese Vorgehensweise empfehlenswert. Die hier erzeugten Bauteile wurden mittels
SLA-Verfahren (Stereolithografie-Verfahren) erzeugt. Bei beiden Modellen wurden sämtliche
Bauteile mit Ausnahme der Federn als Kunststoffmodell gefertigt.
Messtechnik
Zu Beginn des Projektes wurde angenommen, dass auf bereits vorliegende Messtechnik
zurückgegriffen werden
kann. Diese Annahme konnte im Verlauf des Projektes nicht bestätigt werden. Aus diesem Grund
wurde für die zu tätigenden Untersuchungen ein neues Messsystem beschafft.
Bei dem ausgewählten Messsystem handelt es sich um das OptoNCDT System der Firma Mikro
Epsilon. Für die Messungen wurde der ILD1320-10 Sensor ausgewählt. Der Vorteil dieses
Messsystems besteht in der einfachen Integration in die vorliegende Messumgebung. Mit einer
Abtastrate von 2kHz und einer Auflösung von 1µm erfüllt
das Messsystem die von uns gestellten Anforderungen. Das Messsystem arbeitet nach dem
Lasertriangulationsverfahren. Das bedeutet, dass der Sensor die Bewegung eines bestimmten
Körpers detektieren kann. Im Fall des linearen Aktuators ist dies die Position des Kolbens
des
Aktuators. Im Falle des rotatorischen Aktuators ist dies die Position der Welle.
Bau des Prototypen des Hochgeschwindigkeitsaktors
Aufgrund der guten Vorbereitung mussten hier lediglich die Konstruktionsmappen der beiden
Aktuatoren der mechanischen Fertigung zur
Verfügung gestellt werden. Besondere Vorkommnisse/Probleme sind bei der Umsetzung dieses
Meilensteins nicht aufgetreten jedoch hat sich die geplante Bearbeitungszeit um 2 Monate
verlängert. Dies ist auf die Fertigung des linearen Aktuators zurückzuführen.
Zur Optimierung der Reibung wurden Bauteile mit einer speziellen Oberflächenbeschichtung
versehen. Dabei handelt es sich um eine Diamond like Carbon DLC-Beschichtung. Diese
Beschichtung hat das Ziel den Verschleiß zu minimieren und geringere Reibwerte zu
ermöglichen.
Praktischer Test der Aktuatoren und Bewertung
Diese Untersuchungen haben eine Aussage bezüglich des
dynamischen Verhaltens der Aktuatoren unter dem Einfluss des erworbenen Piezosystems zum
Ziel. Dazu wird das dynamische Verhalten des Prototypens mit Hilfe des Sensorsystems
analysiert.
Das Forschungsprojekt „Vollvariable Drehschiebersteuerung für Verbrennungsmotoren“ startete mit der Entwicklung des Hochgeschwindigkeitsaktuators. Die Entwicklung dieses Aktuators wurde in einem Zeitraum von 2,5 Jahren durch den Europäischen Fonds für regionale Entwicklung gefördert. Wir bedanken uns an dieser Stelle noch einmal ausdrücklich für diese Unterstützung ohne welche die Entwicklung des Aktuators nicht möglich gewesen wäre.