Passive vehicle safety
Research projects
Safe(F)light
Safe(F)Light - Innovative safety seat for greater occupant protection in small aircraft
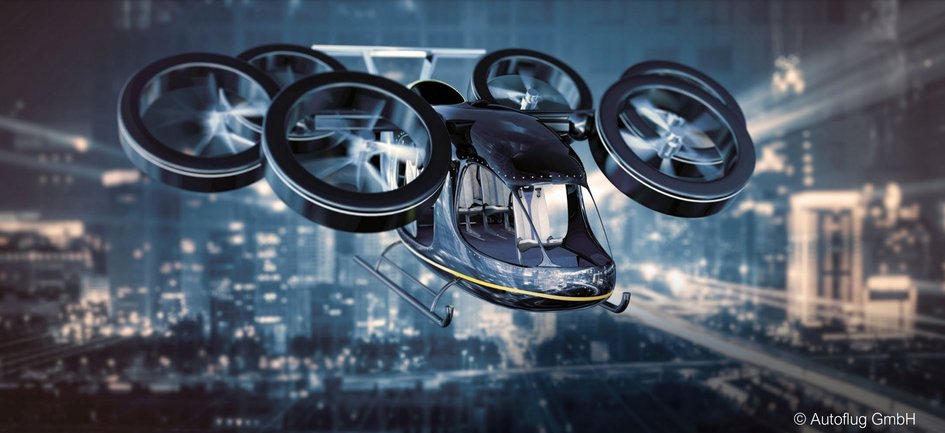
The project:
- Project start: 2022
- Duration: 24 months
- Project partners: 4
- Funding volume: €800,000
- Innovation network: PREVON - Production Evolution Network
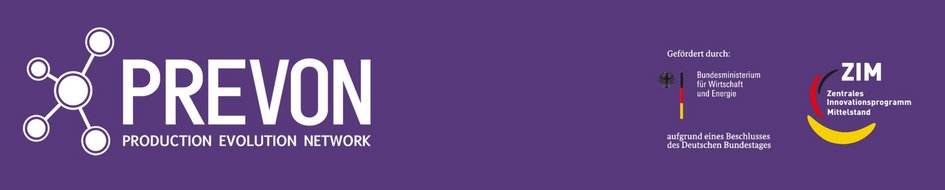
As a highly specialised supplier to the international aerospace industry, Autoflug GmbH is contributing its decades of experience in seat production to the project. Leichtwerk AG is providing its expertise in the development of complex and lightweight system components for the aviation industry. The two companies are supported in the development, production and testing of fibre composites by the Faserinstitut Bremen e.V. and in the area of vehicle safety and crash tests by the Institute of Vehicle Construction at the Ostfalia University of Applied Sciences.
Development of a modular, energy-absorbing seat belt system
Crashes involving small aircraft are life-threatening and often fatal. The existing seats in small aircraft are usually rudimentary seat shells without an energy-absorbing function.
The aim of the "Safe(F)Light" project is therefore to develop a new type of seat belt system for small aircraft. This system is intended to significantly reduce the risk of serious or fatal injuries in the event of a crash by means of a global safety concept based on local, optimally coordinated energy absorption functions.
The main functional features of the "Safe(F)Light" concept to be implemented in the project are a safety and weight-optimised seat frame and an energy-absorbing and adaptive belt system. By integrating functions and largely substituting metallic materials with modern fibre composite materials, the optimised energy absorption is to be combined with the strict space and lightweight construction requirements for small aircraft. A modular, modifiable structure and an efficient manufacturing process should ensure that the innovative seat and harness system is suitable for broad market access and can be used both in the classic small aircraft and helicopter segments as well as in the promising future market of urban air mobility (UAM). In this context, a simulation-based validation method is also to be developed so that the subsequent qualification and approval process can be carried out as efficiently as possible.
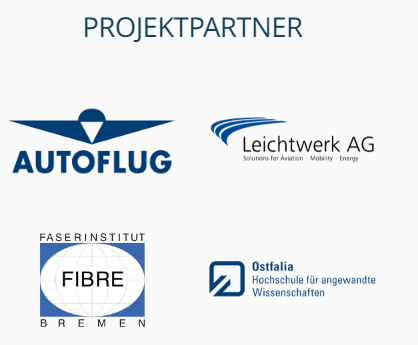
MeSoKKo
MeSoKKo - Method and software development for the production of plastic components
Project management:
Prof. Dr.-Ing. Harald Bachem (opens your email program)
Duration:
01.02.2016 - 30.07.2018
Funding by:
Federal Ministry for Economic Affairs and Energy
Field of research:
Vehicle construction, plastics and materials science (external link, opens in a new window)
Co-operation partner:
ACE Advanced Composite Engineering GmbH, Salem-Neufrach
Project description:
As part of the project, a technology is to be pursued with which components can be manufactured using a combination of sheet moulding compound (SMC) semi-finished products with pre-impregnated continuous fibre reinforcements, which are processed into a complex component in a single-stage pressing and curing process. The focus here is on components that are used in aircraft interiors. The innovative hybrid fibre composite technology is characterised by the realisation of geometrically complex, highly integral and functional lightweight components with extremely short process times in the range of 30 to 180 seconds. This corresponds to less than 10 per cent of today's curing times for pre-impregnated semi-finished products typically used in aircraft interiors
pre-impregnated semi-finished products typically used in aircraft interiors. This application addresses the problems of conventional SMC technology that have prevented its use to date. With a targeted design of the areas with continuous fibres in the components, the problems of mechanical properties and
Mechanical properties and the scattering of parameters in non-directional long fibre reinforcement can be addressed.
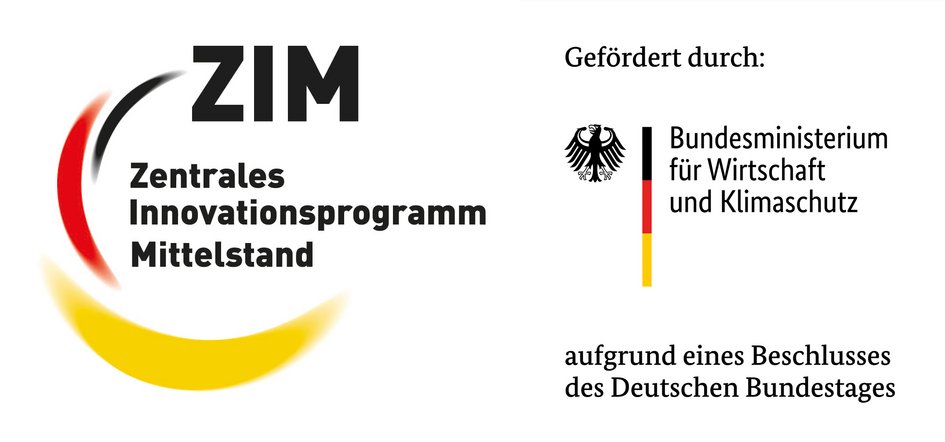
FAKOSI Network
FAKOSI - Ride comfortably and safely!
The LFF is a member of the FAKOSI innovation network, which focuses on the development of innovative comfort and safety technologies for light electric vehicles (LEV). The term LEV describes a wide variety of vehicle types below the passenger car class. In addition to two- and three-wheeled motor vehicles and light four-wheeled motor vehicles, the term LEV also includes e-bikes, pedelecs and other pedal-powered vehicles, such as electrically assisted cargo bikes and other vehicle concepts from the field of micromobility such as e-scooters. In order to address specific development needs, FAKOSI combines expertise in manufacturing processes, materials science, lightweight construction, metrology and other scientific and technical disciplines with medium-sized manufacturers and service providers from the fields of machine vision, embedded systems and AI.
The thematic focus "Passive safety systems for occupant and pedestrian protection" includes the development of technologies for new airbag systems for LEVs, innovative material combinations and crash elements in sandwich construction and component-integrated lighting systems.
Occupant protection for aircraft
Drop tower test Seat structure for eVTOL
Your cookie settings have blocked this video.
Aircraft crash test ULtrasafe
Your cookie settings have blocked this video.
Dynamic load tests for energy-absorbing elements
Drop tower test longitudinal beam
Your cookie settings have blocked this video.
Drop tower test CFRP energy absorber
Your cookie settings have blocked this video.
Drop tower test rig (large)
- Drop masses from 300kg to 1000kg
- Drop height approx. 20m
- Piezo-electronic force absorption
3-axial up to max. 1000kN at 10kHz - High-speed video technology
- Force, displacement and acceleration measurement technology
for recording the deformation behaviour - Laser displacement measuring system
- Acceleration measurement technology
- Impact speeds of up to 64 km/h
Drop tower test rig (medium/small)
Pedestrian protection test bench
Climate chamber
Pendulum test bench
- Impact speeds up to 12km/h
- Adjustable pendulum mass 700kg to 3500kg
- Optional force measurement up to 400kN
- Speed measurement with light barrier system and high-speed recordings
- Customised geometry of the impact nose can be displayed
- Displacement measurement via laser triangulation system
- High-speed video technology